
- Pcad 2001 pcb reference design how to#
- Pcad 2001 pcb reference design software#
- Pcad 2001 pcb reference design professional#
- Pcad 2001 pcb reference design free#
To read more about each tool, click on the page links in table of contents at bottom of each page.
Pcad 2001 pcb reference design free#
The package comes in two versions with a free base-platform with basic options and a paid version equipped with more functionality in terms of error reduction and increased integration flow from schematic to testing.Ĭlick on the image below to begin a quick slideshow (slideshow opens in a new tab on your browser). This includes options for design validation and gives users flexible layout options even with 4-layer PCBs with up to 1400 pin designs.
Pcad 2001 pcb reference design software#
The software is actually part of a larger conglomerate - the NI Circuit Design Software package, which allows users to design their own circuits (circuit capture) and run simulations using a SPICE-based app to test the designs on the fly. One of the better-known tools on the market for both circuit design and simulation comes from National Instruments with their Multisim (formerly Electronics Workbench) platform.
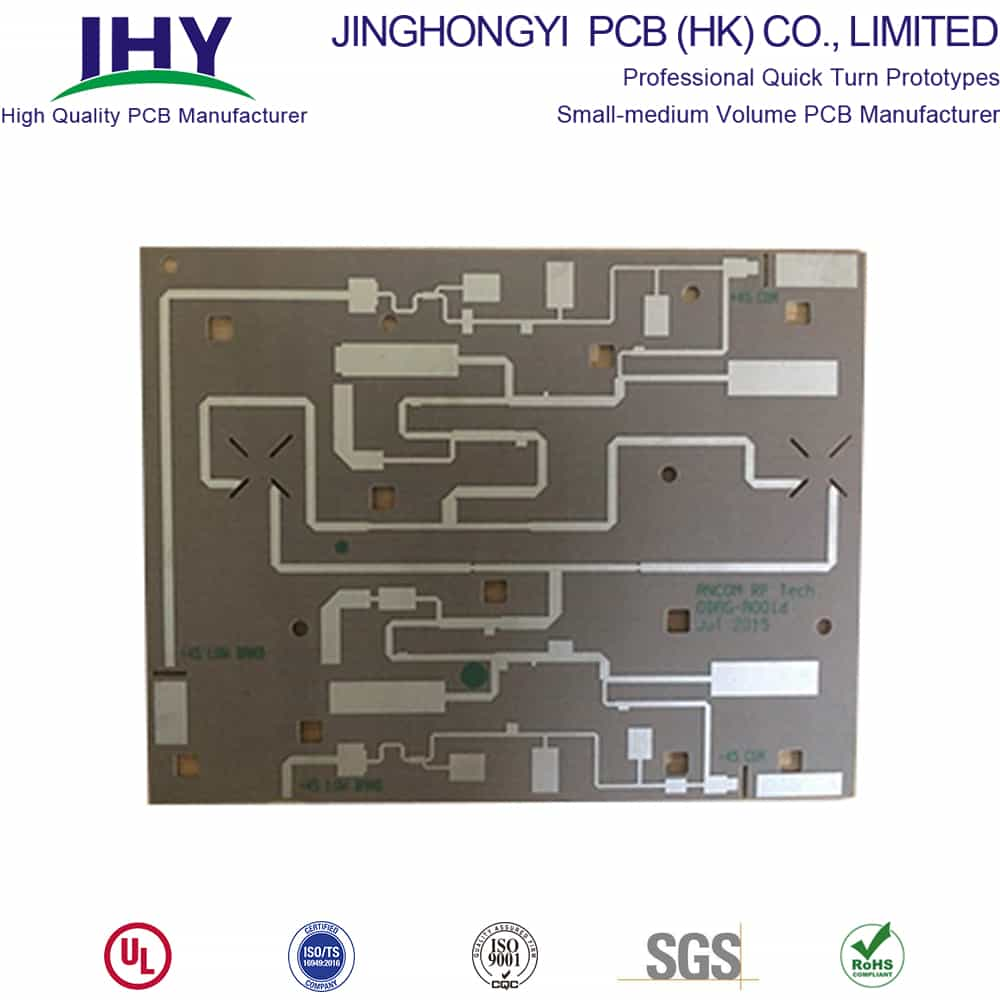
These software packages cost money but can save you costly mistakes. Here are some popular tools to do virtual testing. In other words, make a digital (virtual) prototype of your board and simulate (model) how it will behave in the real world. It’s best to test your design out virtually. Testing can save you money and time avoiding faulty PCB fabrication because it gives you a chance to fix what doesn’t work before the board is made.
Pcad 2001 pcb reference design professional#
For the initial design the path resistance from the VRM to U1 was 18.3 mΩ, and for the improved design it dropped to 9.093 mΩ.Whether you’re a professional printed circuit board designer or do-it-yourselfer, you know that testing your circuit board design is a must. In addition to the power loss, voltage drop and current vector results, the path resistance between sources and sinks was calculated. The original power dissipated due to joule heating within the PCB was ~1.2 Watts but, due to the simple design change, the power dissipated was reduced to ~0.6 Watts. Another significant advantage is the power dissipated on layer 1 was almost cut in half due to the addition of the copper flood in the improved design.
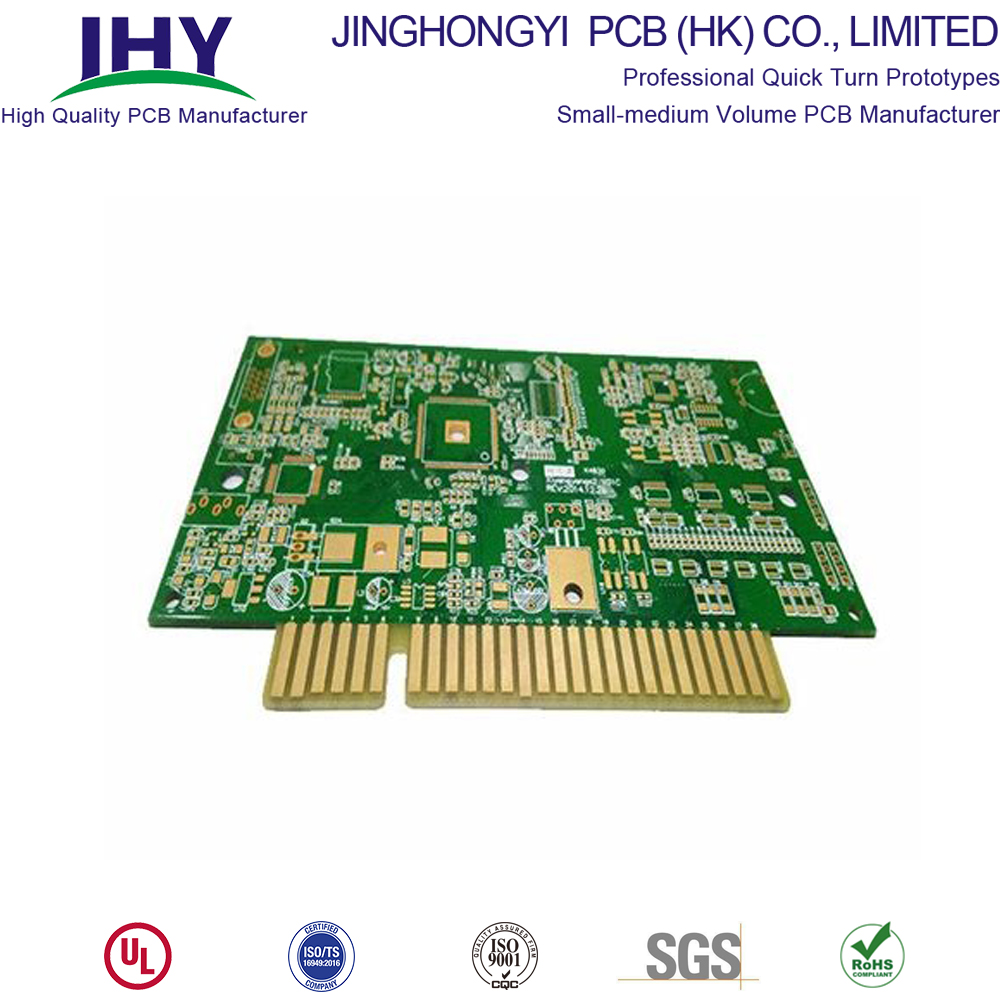
This improved design shows a better current distribution resulting in less voltage drop at the farthest CPU (U1). copper flood on layer 1 along with an additional 10 via transitions from layer 1 to layer 5. The improved design shown in Figure 1 added a ½ oz. The improved design shows an improvement of 70 mV (~8% voltage drop to ~4% voltage drop) at the farthest CPU (U1). The voltage gradient goes from 1.8 VDC to ~ 1.65 VDC. The bottom pictures show the voltage gradient on the Vcc plane.

The cutout view in the upper right shows a comparison between the initial layout and the improved layout where a copper flood and multiple via transitions from layer 1 to layer 5 were added. In addition, layer 1 dissipates ~1.2 watts of power which must be reduced to meet the supplied specification.įigure 1: Upper left shows the location of the VRM and the two CPUs. This results in 8.3 amps through the single via, causing the farthest CPU (U1) to see a 150 mV (~8%) voltage drop. Vcc has only one via transition from layer 1 to layer 5. The initial layout brings power from the voltage regulator module (VRM) through an inductor to each of the CPUs. Using the ANSYS® SIwave-DC simulation tool, we can predict DC power loss and voltage drop for a PCB and then use those results to improve the PCB layout prior to fabrication.įor example, in the design in Figure 1, the Vcc power rail supplies 1.8 VDC power to two CPUs (U1 and U2). It is often necessary to predict the DC performance of power rails to ensure that enough via transitions exist and adequate copper weighting (½ oz, 1 oz, 2oz, etc.) is present to minimize voltage drops during turn-on events and normal operation. Prediction of the PDN performance is critical to ensure consumer electronic products function as specified and meet battery life expectations.
Pcad 2001 pcb reference design how to#
In this product-how to, ANSYS’ Steve Pytel explains how to use the ANSYS SIwave-DC simulation tool to predict DC power loss and voltage drop for a PCB.Īs supply voltages continue to decrease and transistor count follows Moore’s law, power delivery network (PDN) integrity has become an important consideration for any electronic package or PCB design.
